What is
Precision Investment Casting?
Precision Investment Casting, often known as lost wax casting, is a method of forming metals into various shapes by utilising wax and ceramics as a mould. This is one of the oldest known metal casting methods, having endured the test of time for millennia.
Production capacity per annum
Our
solutions
Alloys We Make
➣ Low Alloy Steel
➣ Plain Carbon Steel
➣ Tool Steels
➣ 300 Series Stainless Steels
➣ 400 Series Stainless Steels
➣ Nickle-Based Super Alloys
Surface Roughness & Job Size
Surface Roughness:
3 to 6 microns Ra, possible improvement up to 1.6 microns..
Job Size:
Linear – Within 400x250x150mm
Dimensional Accuracy
Normal:
- within ±0.2 mm for 25 mm, ±0.20 mm for each additional 25 mm
Premium:
- within ±0.15 mm for 25 mm, ±0.08 mm for each additional 25 mm
- 3.00 mm for Low Alloy & Carbon Steel
- 2.50 mm for High Alloy & Stainless Steel
How Does The Casting Process Work?
- We use State-of-Art LOST-WAX Process Technology to bring out the finest precision castings manufacturers.
- The process begins with producing wax replicas of final casting by injecting wax into a metallic die. The patterns are fastened by the gate on a wax runner to form an assembly.
- Tree of wax patterns assemblies is given ceramic coats. The entire assembly is dipped into a liquid ceramic slurry and then coated with fine ceramic sand.
- After the ceramic shell is dry, the wax is melted out, leaving the ceramic shell containing the cavities in place of wax patterns. Melted metal is poured into this shell by gravity pouring.
- The ceramic shell is then knocked out, and castings are separated from the gating system.
- Finally, the casting goes through visual inspection and minimum finishing/machining to deliver the High Quality finished component.
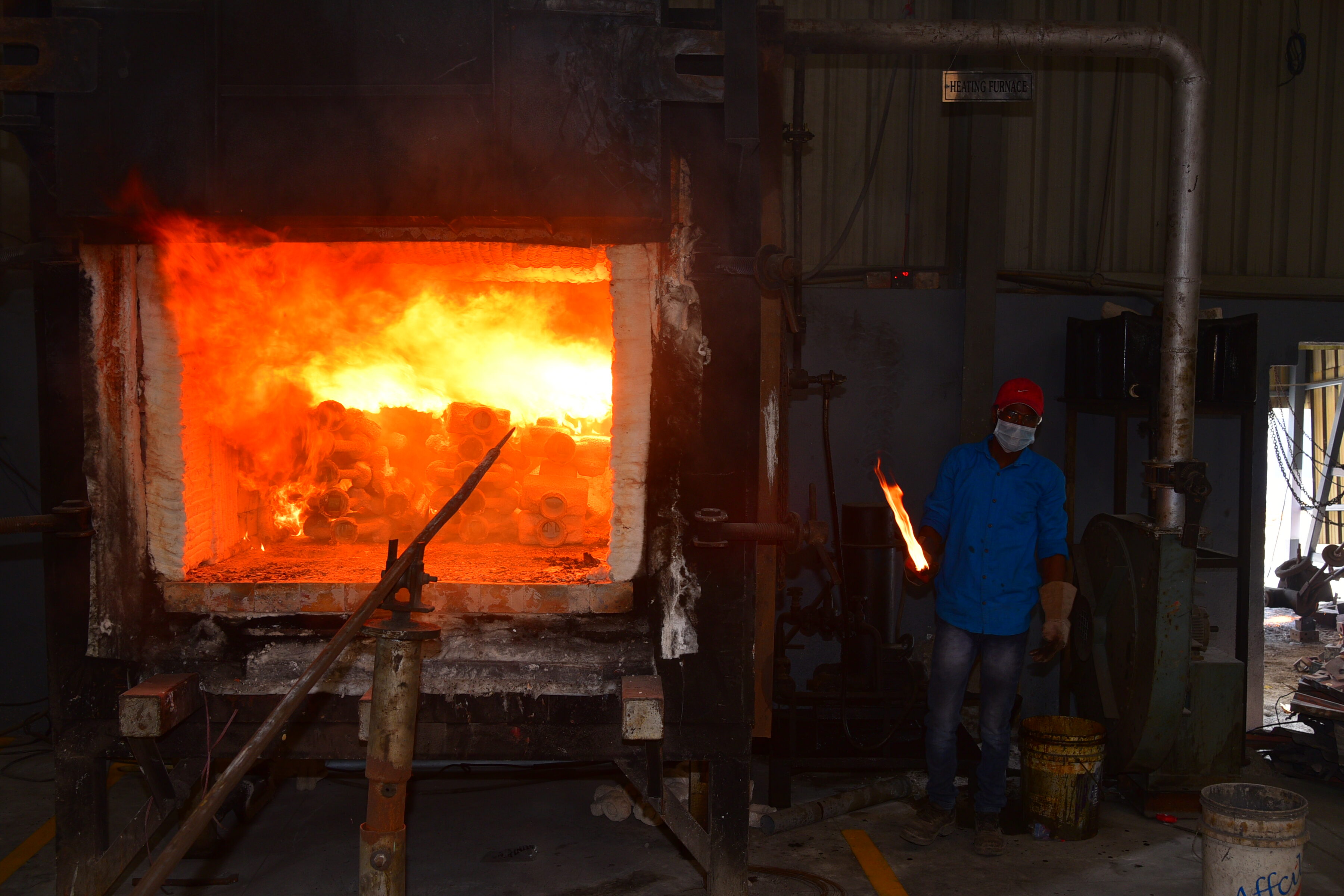